Table of contents
Sometimes, you might receive a batch of components in suspect or reused packaging. Other times, components may have sat out for a bit too long before kitting or assembly. With some components, this is not a problem and will not create difficulties in assembly. Other components that have some sensitivity to moisture could create soldering difficulties or defects, and these will require some baking process before the components can be used.
Some components are assigned moisture sensitivity level (MSL) ratings and they will require additional environmental protection above simple ESD-safe bags. Aside from the additional environmental protection, they may also require baking to remove excess moisture and ensure reliable assembly.
Reliability Problems With Moisture Adsorption
Electronic components that have an MSL rating have a specification called floor life; when the component is exposed to a humid environment for longer than a certain time period, then the components will need to be baked to remove any adsorbed moisture.
There are several reasons to perform a baking process prior to assembly whenever components are exposed for longer than their floor life:
Popcorning: A common defect that can arise in moisture-sensitive ICs during assembly is referred to as "popcorning." This is most often observed in ICs that are packaged on an organic substrate or interposer. During the rapid heating process that occurs during reflow soldering, trapped moisture rapidly expands as it begins to desorb substrate. The fast expansion and desorption creates mechanical stress on the surface coating, and at interfaces between the substrate and molding.
The example below shows how popcorning can arise at the plastic molding-substrate interface.
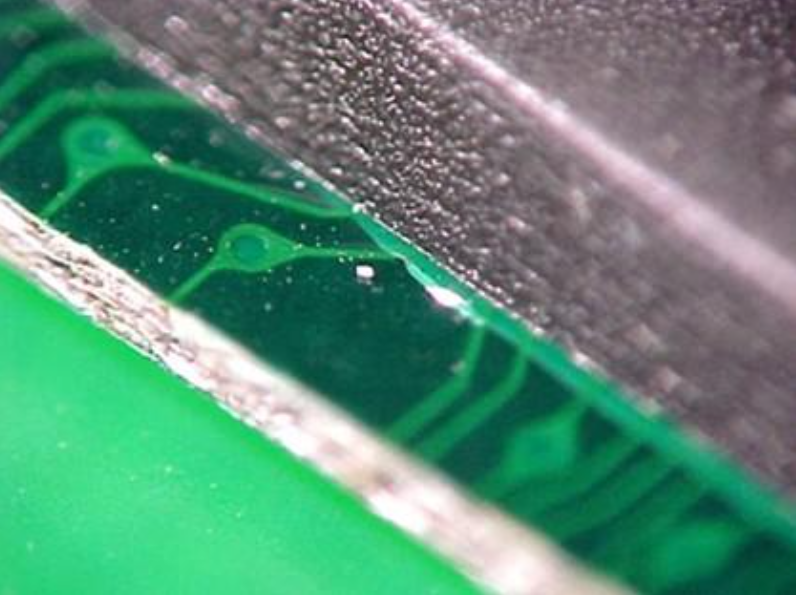
In plastic or epoxy packaged components without an organic substrate, popcorning could take a different form. Rapid heating of trapped moisture can create cracks on the casing. In severe cases, this can expose the interior of the component to the environment.
Solderability: Water can adsorb into surface plating on exposed leads on integrated circuit packaging. When excess moisture adsorption occurs on conductors, it could increase difficulty in soldering and wetting, which might lead to weak solder joints. When some moisture remains in the alloy, it will influence intermetallic growth in the solder joint, potentially creating the following problems:
- Oxide growth
- Voiding in the bulk material
- Brittle intermetallic growth
All of these are undesirable because they reduce the reliability of solder joints to thermal cycling, mechanical shock, and vibration.
Corrosion: Another issue with moisture adsorption in component leads is corrosion. Over time, remnant moisture can oxidize component leads and lead to accumulation of metal oxides along the surface. This appears as a tarnish on the surface of the component leads. In the case where leads are close to the PCB surface, such as BGAs or QFN packages, this might also encourage dendritic growth, especially when the PCB also has excess trapped moisture.
To determine whether your components will be at risk of these reliability problems, read our other article to learn more about MSL ratings for electronic components.
Baking Process for Components
Moisture removal prior to assembly is accomplished with simple baking near the boiling point of water. The goal is to gently encourage water to desorb from component surfaces, which will minimize damage to exposed materials in the packaging. Common baking temperatures range from 100 to 125 °C in a dry environment, but baking could proceed in other conditions.
The table below shows typical baking conditions used at various temperatures. If the baking time at a low temperature is too long, then a higher temperature from this table can be used.
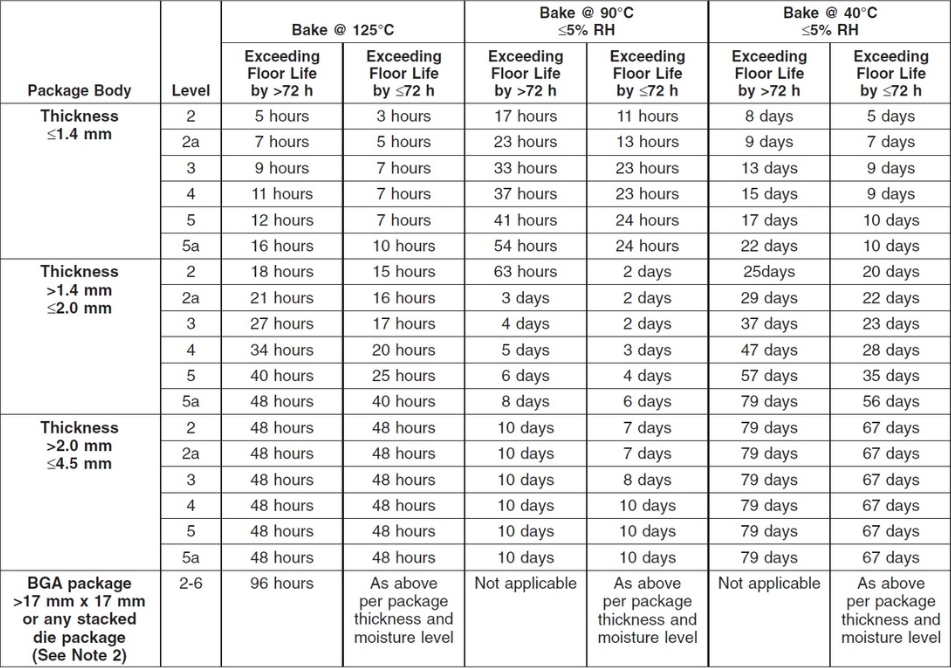
While baking is typically brought up in terms of moisture adsorption while handling on the factory floor, moisture adsorption can also occur in transit if incorrect packaging is used, or if packaging is damaged in transit. Component manufacturers will typically include a moisture indicator card that is compliant with IPC/JEDEC J-STD-033 specifications; this card should be included in the parts packaging and it will provide a visual indicator as to whether the components were exposed to excessive moisture during transit. The card should also identify the manufacturer, part number, and lot number.
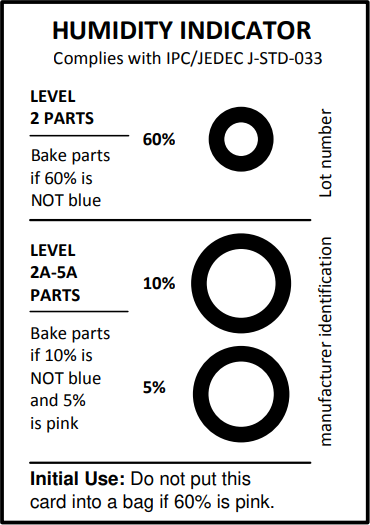
MSL Rated Components From Distributors
Authorized electronics distributors know how to handle MSL rated parts, and they understand the importance of handling components within their allowed floor life. However, parts resellers and brokers may not follow the best practices for packaging and handling moisture sensitive components. They might also re-pack components incorrectly, leading to environmental exposure. As a safety precaution, consider baking moisture-sensitive components received from distributors.
3PL services that specialize in electronic components know how to manage and track floor life for moisture-sensitive components, both during inspection and kitting. If you are using a 3PL to manage your component orders, make sure you deal with one that specializes in the electronics supply chain.
Don’t take your chances with broker networks or distributors, make sure your components are handled and packaged by a reputable platform like Cofactr. Electronic design teams and procurement professionals use Cofactr to quote, purchase, manage inventory, and manage logistics for their electronic components. Cofactr also provides testing, inspection, warehousing, and logistics management services through its online platform.