Table of contents
Electronics production and semiconductor manufacturing are cyclical businesses that wax and wane with broader economic trends. 2020-2021 was an extraordinary period where extreme demand combined with labor shortages produced the current semiconductor shortage we’ve been dealing with over the recent past. The situation was so bad that it sparked an onshoring and investment movement among semiconductor vendors and electronics manufacturers, the likes of which have not been seen in the recent past.
Unfortunately for semiconductor manufacturers, drops in demand coincided with refocused production efforts and the construction of new semiconductor fabrication capacity. Today there is a huge inventory glut amounting to billions of dollars of integrated circuits, passive components, discrete semiconductors, and popular consumer products. Now that the electronics supply chain situation has flipped into excess, should you change your inventory management and sourcing practices to adapt?
Inventory Management Through a Surplus
When the rest of the electronics supply chain is in a state of surplus, your goal in inventory management is to prevent your facility from also accruing excess inventory. If your company is already holding excess inventory, the same goal applies and you should try to ensure you do not accrue even more excess parts inventory. There are two simple steps that can be taken within the new just-in-case supply chain management paradigm:
- Partial BOM orders - If you’re restocking for an upcoming production run, you might not need to order the entire BOM. Order just the portion of the BOM you need so that you can work off some of the inventory.
- Set reasonable buy triggers - Instead of buying 2 or 3 production runs ahead, buy 1 run ahead. This gives you a chance to work off your own excess inventory, and you’ll still have low buying risk when supplies with distributors remain high.
It’s important to hold some inventory to ensure you can continue producing, but excess inventory with distributors allows you to take these ordering steps with lower risk than in times of shortages. Aside from these points regarding ordering, something still needs to be done with excess inventory in your own facility.
What Can You Do With Excess Component Inventory?
If you do find yourself with excess inventory, especially parts for an older product, what should you do with these parts?
Prioritize Parts in a New Design
Finally, you could prioritize these old parts in a new product. For some parts (passives, common ASICs), this is quite easy and it makes a lot of sense as old design data can be reused in a new project. For other parts it’s not so simple because those parts could provide very unique functions. Having inventory visibility is important here because it will show you exactly how much of your old parts you will use in the new product.
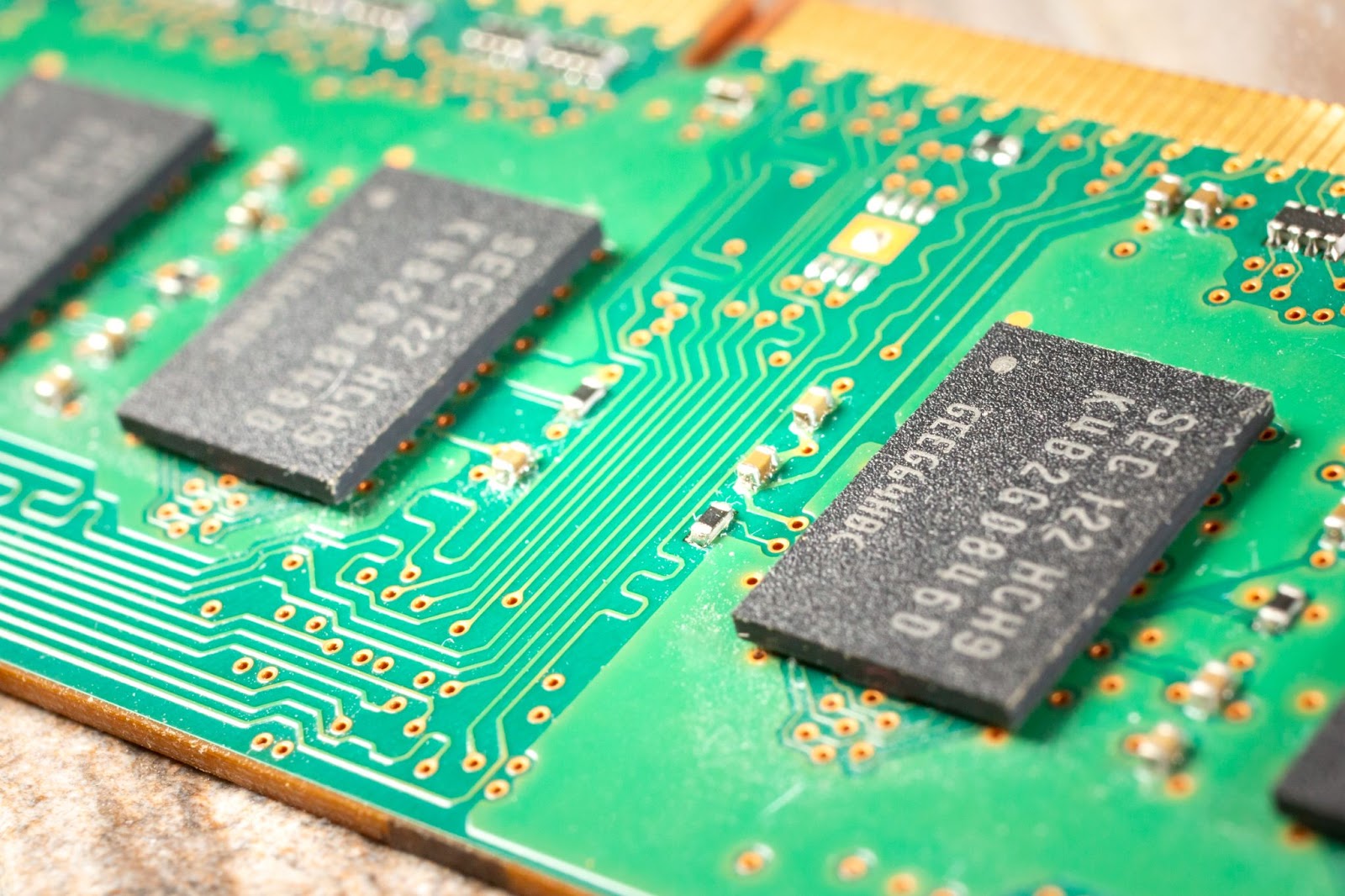
Become a Broker
While some may have some ethical or moral qualms with this, you could resell your old components to another distributor. Some distributors will do a trade at the market price, so you could swap for a component you need for a new design. Don’t cast suspicion on yourself by doing this; make sure you can provide documentation that shows from where the components were procured and when they were purchased (usually a receipt).
Package and Store Everything
If your company is holding excess inventory, the simple option is to package and store everything long-term. Electronic component packaging for long-term storage is very simple and is similar to the packaging used for shipping components and assemblies. For components that have an MSL rating of 2 or higher, you will typically need more rugged packaging that is rated to withstand higher humidity levels. A controlled storage environment is also recommended.
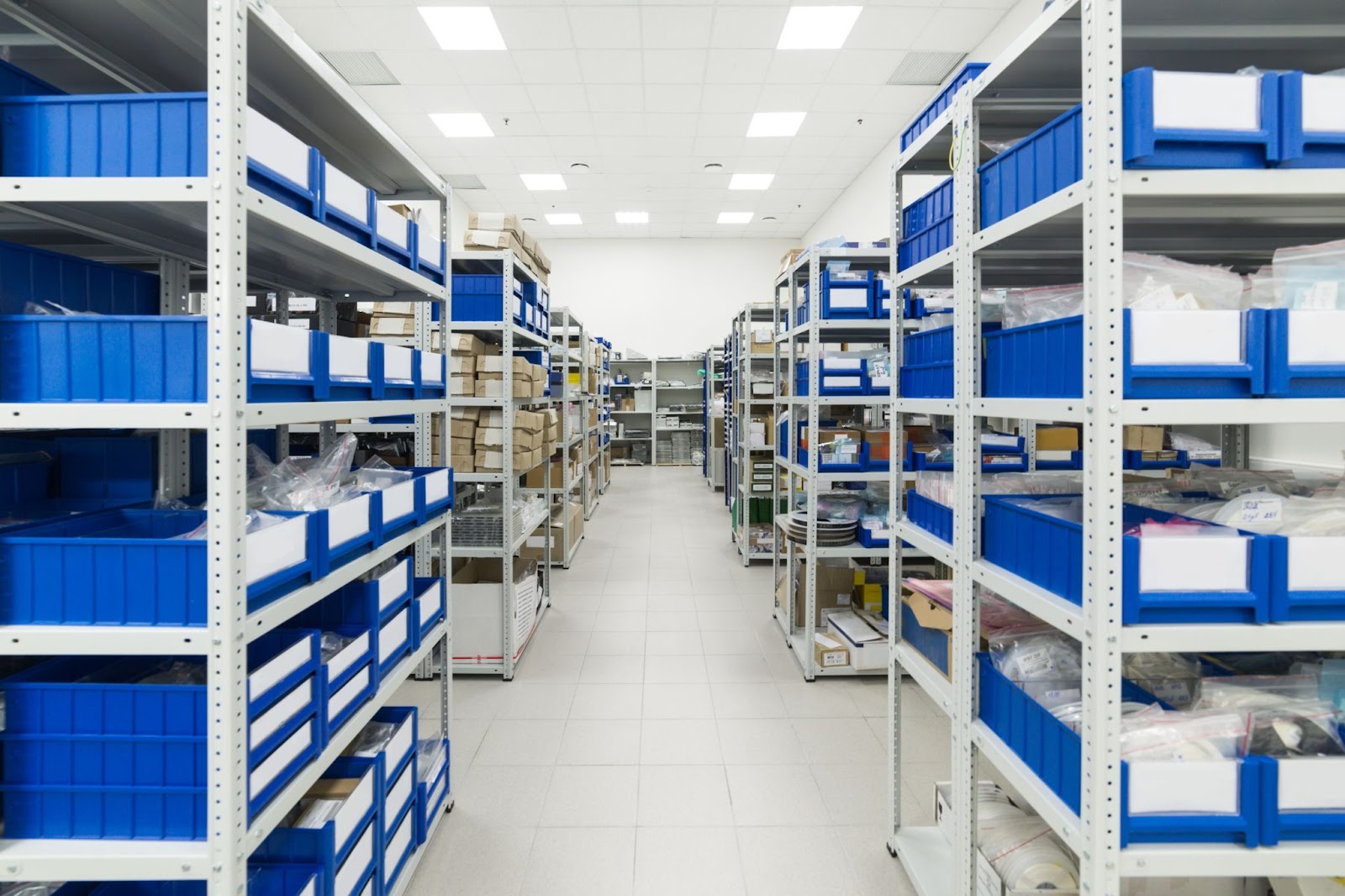
Will Just-in-Time Make a Comeback?
During the depths of the most recent semiconductor shortage, which spanned just about everything from discrete semiconductors and high-compute processors, many supply chain professionals declared the death of just-in-time inventory management. This wasn’t just the case for electronics manufacturing and sourcing; industries ranging from seafood to textiles were making the same pronouncements. Because the shift in mindset to just-in-case supply chain management is so widespread, don’t expect companies to revert back to just-in-time logistics any time soon.
Once producers and distributors across industries adopt a widespread focus of prioritizing inventory management, it’s difficult to see how an entire industry will shift back to just-in-time practices. However, in the near term, smaller companies who consign components for assembly do have an opportunity to go back to their just-in-time ways. Smaller volumes will bring lower risks in times of excess inventory, so smaller companies can get away with a just-in-time sourcing strategy for low-volume production runs.
Whether you want to take a just-in-time or just-in-case approach to inventory management, you can use a platform like Cofactr to implement your supply chain management strategy. Electronic design teams and procurement professionals use Cofactr to quote, purchase, manage inventory, and manage logistics for their electronic components. Cofactr also provides warehousing and logistics management services through its online platform.