Table of contents
When you take a look at your BOM, obsolete parts could be lurking within. Without continuously scanning distributor sites or using a 3PL provider for electronics, you might not notice the obsolete parts cropping up in your PCBA. OEMs have taken many steps to implement obsolescence management processes and integrate lifecycle data into their PLM systems in order to ensure products can be maintained throughout their lifetime, so it would seem the problem can resolve itself without undue costs.
The reality is that obsolescence issues create significant overhead costs when we examine long-term maintenance of legacy systems. And without a process for addressing obsolescence before a product is deployed in the field, maintenance overhead piles up to the point where it quickly becomes unprofitable. These are the real costs of component obsolescence as they do not get factored into costs before a product is taken to market. Companies can leverage supply chain data and make plans early to ensure product maintenance does not create excessive costs.
Product Cost Drivers Are Related to Component Obsolescence
There are several product cost drivers that are related to electronic component obsolescence.
Product Refresh
- Redevelop sub-components for an in-service system
- How will this be funded?
Service Commitments
- Maintenance schedules - built into service contracts?
- Warranties
- Parts obsolescence could force a product refresh
Projected Lifecycle
- Minimum or maximum lifecycle?
- Drives the length of product service commitments
Component End-of-Life
- Could drive mid-lifecycle redesigns (product refresh)
- Could drive sourcing costs during production
- Counterfeiting risk if using brokers
Among the four issues highlighted in the above table, three of them can be influenced by product design and engineering teams. Engineering teams have no control over obsolescence and EOL scheduling for components included in a design, while the other issues can be negotiated with customers and considered early in design cycles. The biggest problem with component obsolescence/EOL is that it can suddenly increase costs in any of the other three areas.
When product lifecycles are longer, expect overall product costs to increase due to greater overhead. Eventually, when a product’s lifecycle is particularly long, a system will become a legacy product that still requires maintenance.
Costs of Maintaining Legacy Systems
One of the major cost issues that arises from obsolete components is in maintaining legacy systems, such as in military and aerospace systems. The automotive industry also tends to take a conservative approach and will have a preference for some proven legacy systems in an effort to reduce risk. In other areas, such as industrial systems, legacy system maintenance costs can be unprofitable but still less than the cost of total system replacement.
The problem in military and aerospace is particularly acute because these systems can have lifecycles spanning decades and up to 25% of system overhead goes to legacy maintenance. According to a 2016 US Army press release, millions of taxpayer dollars could be saved through better obsolescence management processes for mission-critical systems. At the electronics level, once the main value-creating components go obsolete or EOL, the product itself is then deemed obsolete. Companies supporting these systems quickly find the practice unprofitable because of repeated redesign efforts.
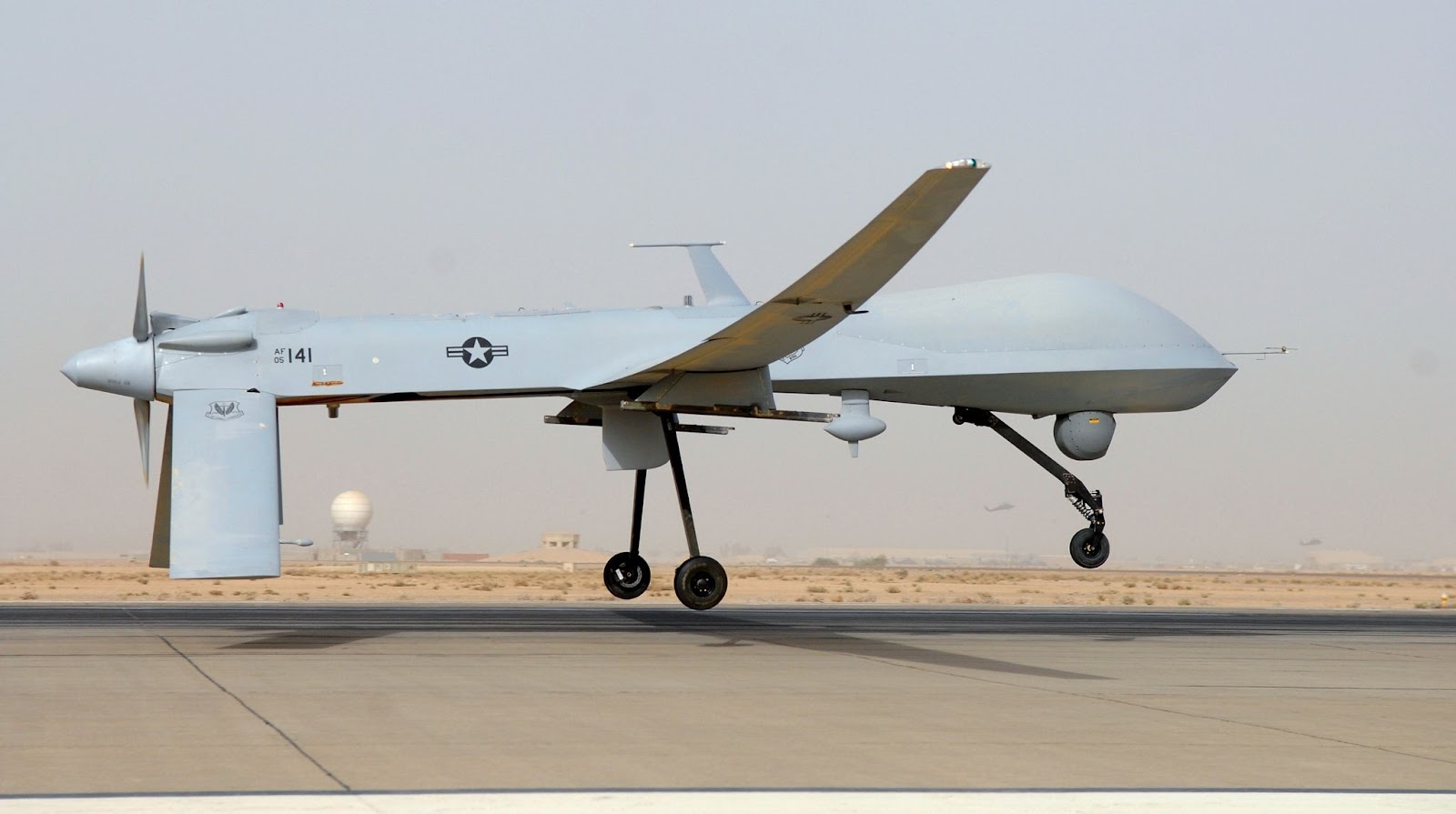
When the lifecycle for a customer’s product is longer, the overhead and maintenance costs will generally be larger as a percentage of sales revenue. Longer product qualification cycles also increase the costs and risks of component obsolescence. These factors must be considered as part of a long-term maintenance plan for a new product.
Plan For Obsolescence and Legacy Maintenance
Given that replacement and maintenance costs can be such a huge driver of overhead, and they lead to sticker shock for customers, what can companies do to reduce their legacy maintenance costs? The problem starts in the design phase, and it requires a recognition of the parts that are most at-risk.
- Eliminate obsoletes early - When the product first goes into production, eliminate any obsolete part before the first production run.
- Create a list of alternates - If you have a list of suitable alternates at the beginning of the product’s lifecycle, you have now front-loaded some of the maintenance costs. An even better practice is to create design variants with the highest priority alternates.
- Last time to buy? Make a plan! - If a component gets marked last time to buy, come up with a realistic maintenance or upgrade plan that accounts for the entire product lifecycle.
- Who’s buying parts? - If your CM is sourcing parts in your design, they have a responsibility to inform your team of obsolescence and EOL. Make sure there is open communication with your suppliers.
Another issue is vendor support. Certain vendors have much better processes for dealing with obsolescence/EOL, issuing parts discontinuation notices, and providing suitably compatible replacements that will reduce redesign and maintenance costs. Larger companies tend to have the staff and processes in place needed to keep customers and distributors aware of EOL issues. This information should filter down into your procurement management and inventory management systems so that you can source sustainably.
Cofactr gives electronic component buyers instant visibility into component specifications and lifecycles so that buyers can manage sourcing for their product lines. Design teams and buyers use Cofactr to quote, purchase, manage inventory, and manage logistics for their electronic components. Cofactr also provides warehousing and logistics management services through its online platform.